We at Paessler have a dream! We have a dream that one day...Okay, let's not make it so dramatic. Thing is: Besides the goal of providing our users with reliable uptime and a full overview of their IT, OT and IoT systems, we have made it our mission to reduce resource consumption together with our customers. It is our belief that monitoring has an essential role to play in reducing the consumption of resources by mankind, and our customers can do exactly this with monitoring data. Certain companies have already shown through great use cases not only in how they use PRTG to monitor their sometimes very complex systems, but also how they manage to fulfill this particular purpose and reduce their resource consumption.
Here is the first use case of this series. Enjoy!
Bosch Rexroth AG develops and produces electric drives with open control systems, which form the basis for intelligent production plants and thus the basis for industry 4.0 plants. Customers from a wide variety of industries around the world can order Rexroth products in 200,000 varieties and variable batch sizes. By converting the Lohr am Main and Erbach plants to an industry 4.0 environment, production became significantly more efficient, both in terms of quality and productivity. For example, both the ordering and ERP systems were linked to the production control system and production. The monitoring solution PRTG Network Monitor is used to ensure reliable operation of the new, complex IT infrastructure.
iAbout Bosch Rexroth and the reduction of carbon dioxide emissions
Clearing snow at -0° F and harvesting corn at +100° F; manufacturing components with 1000th mm accuracy; moving slice gates that weigh several metric tons and the most famous stages in the world – Bosch Rexroth moves everything. As a global partner, Bosch Rexroth supports mechanical and plant engineering efforts around the world with its cutting-edge technology and unique industry knowledge. More than 31,100 associates across the globe are developing tailor-made, safe and resource-friendly solutions. Innovations from Bosch Rexroth deliver multi-dimensional enhancements for machine manufacturers and end users.
Bosch Rexroth helps, for example, to reduce harmful carbon dioxide emissions while increase simultaneously raising productivity. Above all, Bosch Rexroth makes cross-technology automation solutions easy to use through predefined functions and integrated, open engineering tools.
At its LoP2 plant in Lohr am Main and Erbach, Bosch Rexroth manufactures electric drives and controls with open-core control systems (Open Core Engineering). The products manufactured here form the basis for factory automation and industry 4.0 throughout the world. With individual customer requirements and more than 200,000 product variants, networked production, in which the product controls its own production, is not only more efficient, but also significantly less prone to errors. This is the principle of industry 4.0. At Bosch Rexroth, this means that a digital image of the product is created at the start of production by closely linking ERP and MES systems. This virtual product then controls all production steps, which can be carried out paperlessly and without setup times. The smooth functioning of the networked IT becomes a decisive factor in production. In the event of an IT failure, productivity and thus the efficiency of production is at risk. This makes continuous and comprehensive monitoring of the entire IT system indispensable.
Detect problems before they occur
Christian Miceli was jointly responsible for the digitization process of the LoP2 plant. As an internal expert and co-designer of networked manufacturing, he was able to clearly define the most important requirements for the software to be used:
- Monitoring of the two locations in Lohr am Main and Erbach with one Windows-based instance
- Configuration and operation as simple as possible
- Ability to map complex relationships between different components
- Storage and evaluation of historical data
- Easy creation of individual user views and output as a web service
- Integrated notification functions (escalation management)
“PRTG offers the right combination of predefined queries and flexible options for customized add-ons. This makes PRTG ideal for comprehensively and reliably monitoring the complex IT infrastructure of industry 4.0 environments.”
PRTG the clear choice
In order to find the right software, Miceli and his team evaluated several network monitoring solutions. Among all candidates, PRTG Network Monitor from Paessler AG in Nuremberg quickly became the favorite; among other things, because the software allows remote probes to monitor distributed locations from a central installation. The software is based on Windows, and the installation process can be carried out without special knowledge.
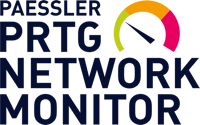
Those responsible at Bosch Rexroth AG were also taken with the user interface. „In addition to many other features, we particularly liked the maps in PRTG: This allows us to quickly and easily create clearly arranged dashboards and display the data that is relevant to each colleague,“ explains Miceli. Bosch Rexroth also needed German-language support and regular updates for the product. The implementation went as expected without any incidents.
Monitoring under Industry 4.0 conditions
In the meantime, the upgrade of the LoP2 plant to an industry 4.0 environment has been completed and the entire production process is networked. PRTG makes a significant contribution to the organization and stability of the two locations Lohr am Main and Erbach. In addition to a large number of predefined queries for devices and applications, so-called sensors, PRTG offers an API and custom sensors. These are templates that enable the uncomplicated integration of customer-specific devices and applications into PRTG using individual scripts.
For example, Bosch Rexroth collects humidity and temperature data from various sensors using SNMP. The results of the sensors are combined in a so-called PRTG Sensor Factory. This can combine several PRTG sensors within one sensor. The results of the various sensors can then be individually weighted using the user‘s own calculations. „Using our own formulas, we can use the Sensor Factory to precisely define notifications and alarms based on complex environmental conditions,“ explains Miceli. PRTG also stores all the data it collects. This allows us to perform subsequent evaluations, react to trends and optimize our production environment over the long term.
Shortly after implementation, Paessler AG‘s solution monitors not only temperature and humidity, but also large parts of the IT infrastructure. These include, for example, physical and virtual servers, PCs, office printers, NAS (Network Attached Storage) and the uninterruptible power supply (UPS) of the systems. Label printers, which are also integrated into PRTG via custom sensors, play a special role. PRTG monitors all these components at both locations and displays the data on the PRTG web interface and enterprise console. Miceli also sees great potential for access to PRTG: „In the next step, we will test the mobile apps for iOS and Android that PRTG offers. We are hoping that this will significantly increase mobility and flexibility of monitoring our IT.“ In the future, PRTG will also monitor the correct execution of backup jobs.
Conclusion
The intelligently networked production in the LoP2 plant has become possible through the use of PRTG. PRTG helps identify malfunctions faster. Future impediments are reduced by long-term optimizations based on the evaluation of historical data. „Paessler‘s solution fully met our expectations,“ says Miceli, summarizing the project. „PRTG offers the right combination of predefined queries and flexible options for individual extensions. This makes PRTG ideal for comprehensively and reliably monitoring the complex IT infrastructure of industry 4.0 environments.“ The decision for a German product was also a good choice: „The support from Paessler AG was as uncomplicated as it was efficient."
😍 Do you have a story to tell...?
... of how you and your company manage to save resources with PRTG? This makes our hearts beat faster. Please contact us and tell us everything! Simply click the banner below or use: resource.reduction@paessler.com